Fabriqué en Autriche : TECTONest toujours l'une des familles de produits les plus populaires du portefeuillede Zumtobel et est fabriqué à l'usine de Dornbirn.Ce n'est pas étonnant, carTECTON était le premier système de chemin lumineux au mondeéquipé d'un railporteur intégré à 11 pôles.. Il constitue la base de l'éclairage général, del'éclairage de sécurité et de secours ainsi que de la commande de l'éclairage.Un rail, des possibilités (presque) infinies.
Mais avant que TECTONpuisse être utilisé par le client comme un système d'éclairage en lignecontinue multifonctionnel, plusieurs étapes de production sont nécessaires.Découper,profiler et câbler les rails en tôle d'acier, fabriquer l'optique de lalentille par moulage par injection, produire l'élément d'éclairage pour le railporteur. Michael Lassak a un œil sur chaque étape de la fabrication. En tantque Production Group Leader au sein du groupe Zumtobel, il est entre autresresponsable de la production de TECTON à Dornbirnet partage trois idéessurprenantes tirées de son expérience « en coulisses ».
#1 L'automatisation rencontre le montage manuel
Une partie de laproduction de TECTON est déjà entièrement automatisée. Mais en réalité, unvéritable montage manuel est aussi demandé aux quelque 80 collaborateurs deTECTON. Ainsi, les rails TECTON sont produits de manière semi-automatique entrois équipes. Les collaborateurs s’occupent de poser les rails en plastique,les machines se chargent du reste de la fabrication et du câblage des rails.
Pour la production del'élément d'éclairage TECTON, les collaborateurs montent manuellement descomposants sur la barre d'éclairage. Ensuite, des cellules robotisées autonomesprennent le relais : Un robot va chercher des optiques de lentilles dans un emballageet les place à l'aide d'une caméra. Un autre robot pose des platines LED.Ensuite, les machines posent la barre lumineuse prémontée, la vissent et lacâblent. Enfin, l'élément d'éclairage est programmé de manière entièrementautomatique. En combinant le montage manuel et les processus automatisés, onobtient par équipe 900 à 1200 éléments pour le système de chemin lumineuxTECTON.
Le travail manuel deprécision, réalisé par des spécialistes bien formés restera particulièrementimportant à l'avenir.: « Car il n'est pas possible de réaliser tous lessouhaits de nos clients sur une installation entièrement automatisée », ditMichael Lassak, Production Group Leader. « Pour nous, il reste indispensabled'avoir chez nous des lignes de montage manuel qui permettent de réaliser desprojets personnalisés ».
Les « luminaires spéciaux», c'est-à-dire les luminaires fabriqués sur mesure selon les souhaits desclients, représentent environ un quart du chiffre d'affaires du site deDornbirn, et la tendance est à la hausse. Les luminaires spéciaux sont unecaractéristique importante de la position unique des experts en éclairage duVorarlberg. « Nous répondons à presque tous les souhaits de nos clients »,explique Michael Lassak, chef de groupe de production. « Presque chaquesemaine, nous avons des constructeurs qui viennent nous voir avec de nouvellesidées et exigences de clients et avec lesquels nous réalisons des échantillons.C'est tout simplement passionnant tous les jours ».
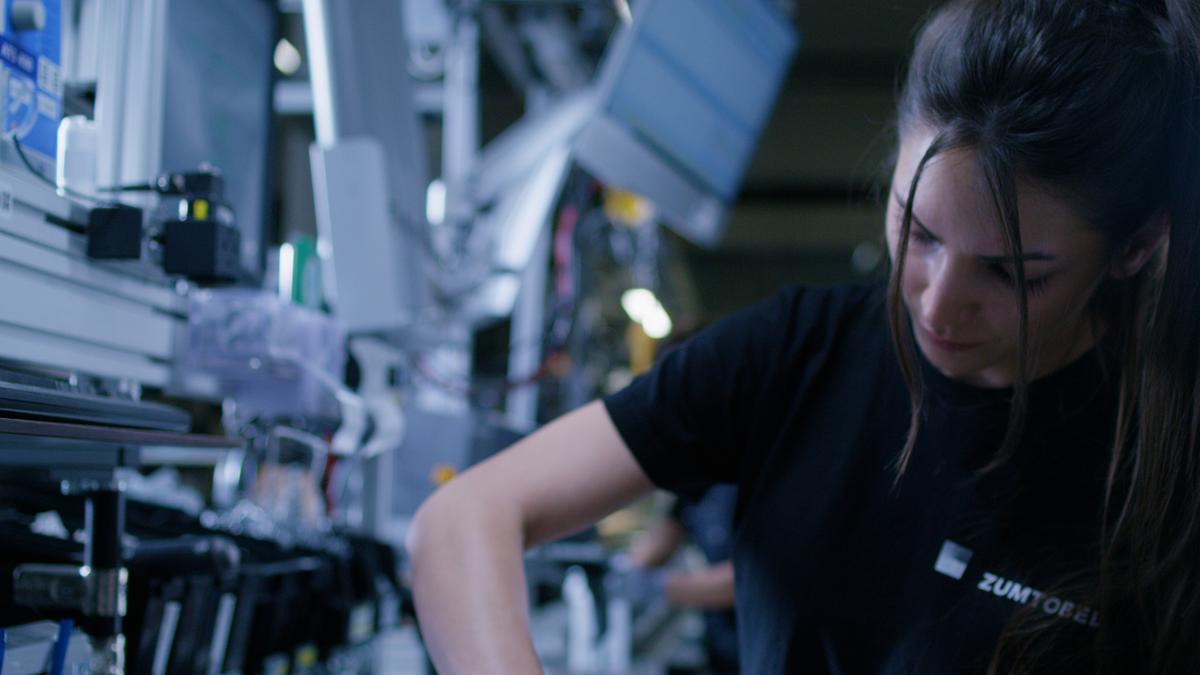
#2 L'exigence de qualité rencontre la vitesse de production
Chaque écart par rapportau standard nécessite également un processus de travail différent. MichaelLassak explique les défis auxquels sont confrontés les collaborateurs de laproduction : « Nous avons parfois besoin d'autres dispositifs de montage, les appareilsde contrôle nécessitent d'autres réglages et nous devons élargir les programmesde contrôle existants ». Enfin, l'exigence de qualité de Zumtobel s'appliqueégalement aux luminaires fabriqués sur mesure pour les clients : Chaqueproduit, comme le promet le client, est contrôlé à 100 % avant de quitterl'usine de Dornbirn. Pour y parvenir, les luminaires Zumtobel ne sont passeulement certifiés ISO à plusieurs reprises. Un concept de « traçabilité »propre à Zumtobel assure une transparence sans faille dans le déroulement de laproduction et crée des normes de qualité obligatoires : Pour cela, chaqueluminaire reçoit son propre QR codequi est enregistré à chaque étape de lafabrication. Chaque pièce intégrée lors de la fabrication,qu'il s'agisse de LEDou de convertisseurs, est préalablement scannée et clairement attribuée auluminaire.
Une partie des contrôlesse déroule déjà de manière automatisée, par exemple le contrôle de qualité del'optique de la lentille TECTON. Zumtobel les fabrique à partir de granulés deplastique selon un procédé de moulage par injection. Pour cela, les granuléssont liquéfiés à 320 degrés, injectés et ensuite pressés. Avant que lesoptiques finies ne soient montées, une caméra optique examine les résultats dela production et veille ainsi à ce qu'aucun composant présentant des impuretés,des inclusions ou des modifications géométriques ne soit monté.
La nouvelle installationde production pour TECTON II, entre autres, prouve que gestion globale de laqualité et vitesse de travail élevée ne s'excluent pas mutuellement. Lanouvelle génération du système de chemin lumineux éprouvé doit être lancée surle marché au printemps 2025 et fixe déjà des standards au sein de l'usine deDornbirn : « Il est prévu que la nouvelle installation produise une fois etdemie plus que l'ancienne dans le même laps de temps », révèle le ProductionGroup Leader Michael Lassak. « La nouvelle version TECTON II est encore plusexigeante sur le plan technique que le luminaire TECTON C utilisé jusqu'ici.Pour la construction de la nouvelle installation et des lignes de montagemanuel, nous nous sommes donc explicitement penchés une nouvelle fois sur lesdéfis du passé et nous nous sommes demandé : Quels enseignements pouvons-nousen tirer ? Comment pouvons-nous organiser la fabrication de TECTON II demanière optimale ? » De vastes expériences acquises pendant plus de 20 ans ontainsi été intégrées dans la configuration de production de l'état de l'art.
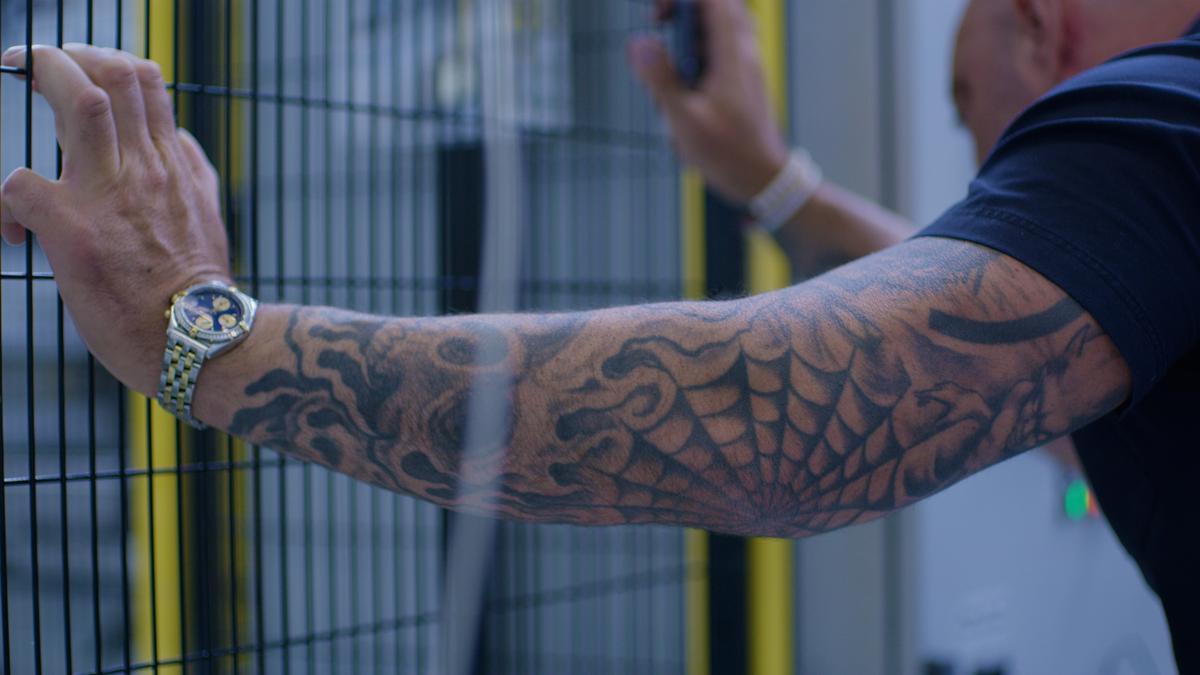
#3 La rééditionrencontre la rétrocompatibilité
Dans l'esprit de ladurabilité, l'ère TECTON II ne coupe toutefois pas les liens avec le passé. Larétrocompatibilité du système, qui convient particulièrement bien aux projetsde rénovation, y veille. Le rail TECTON existant reste, le luminaire actualiséarrive : C'est selon ce principe que Michael Lassak et l'équipe TECTON ont déjàréalisé des projets réussis par le passé : « Un bon client voulait que lesluminaires TECTON C, alors nouveaux, soient adaptés à son système de railsporteurs existant. Un petit défi pour mes collaborateurs et moi-même, car nousdevions marier l'ancien système avec le nouveauet créer un faisceaucorrespondant. Le fait que nous y soyons parvenus a finalement rendu notreclient heureux ».
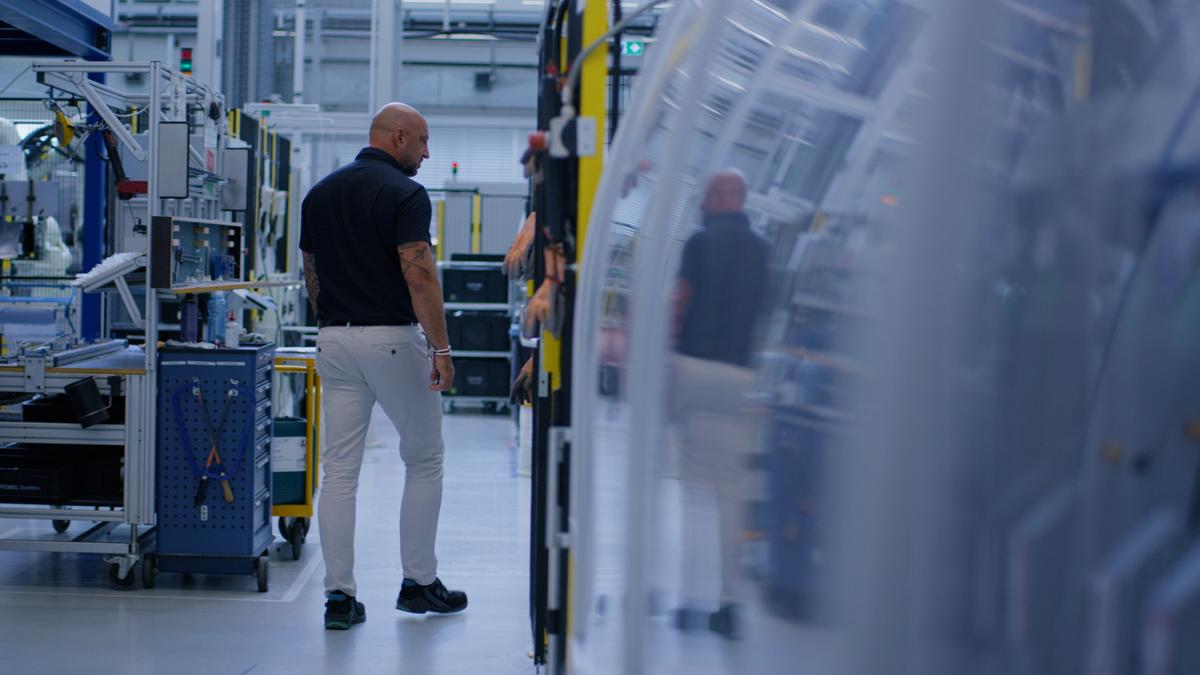
Conclusion : l'orientationinconditionnelle vers le client est maintenue même avec la nouvelle générationTECTON II. Il est d'ores et déjà certain que le luminaire TECTON II estrétrocompatibleet qu'il permet donc d'utiliser les installations existantes demanière absolument sûre pour l'avenir, durable et en préservant les ressources.Automatisation et montage manuel. Exigence de qualité et vitesse de production.Réédition et rétrocompatibilité. Des contradictions apparentes réunies dans unsystème bien pensé : c'est peut-être justement l'un des secrets essentiels dusuccès de la production TECTON à Dornbirn.