Made in Austria: TECTONè ancora oggi una delle famiglie di prodotti più richieste di Zumtobel e vieneprodotta nello stabilimento di Dornbirn. Non c'è da stupirsi, visto che TECTONè stato il primo sistema di file continue al mondo con un profilo conduttore a11 poli integrato nel canale. Costituisce la base per l'illuminazione generale,l'illuminazione di sicurezza e di emergenza e il controllo della luce. Un solobinario, possibilità (quasi) infinite.
Ma prima che TECTONpossa essere utilizzato dai clienti come sistema multifunzionale di filecontinue in loco, sono necessarie diverse fasi di produzione. Punzonatura,profilatura e cablaggio dei binari in lamiera d'acciaio, produzione di otticheper lenti mediante stampaggio a iniezione, produzione di inserti luminosi per ibinari. Michael Lassak tiene sotto controllo ogni singola fase di produzione.In qualità di Production Group Leader del Gruppo Zumtobel, è responsabile, trale altre cose, della produzione di TECTON a Dornbirn e condivide con noi tresorprendenti intuizioni tratte dalla sua esperienza “dietro le quinte”.
#1 L'automazione incontra l'assemblaggio manuale
Parte della produzionedi TECTON è già completamente automatizzata. Tuttavia, i quasi 80 dipendentiTECTON che attualmente vi lavorano devono anche eseguire un vero e proprioassemblaggio manuale. Le guide TECTON vengono prodotte in modo semi-automatico intre turni. I dipendenti inseriscono solo le guide in plastica, mentre il restodella produzione e del cablaggio delle guide viene eseguito dalle macchine.
Per la produzionedell'inserto luminoso TECTON, i dipendenti assemblano manualmente i componentisulla barra luminosa. Poi subentrano cellule robotizzate autonome: Un robotrecupera le ottiche da un contenitore e le posiziona con l'aiuto di unatelecamera. Un altro robot posiziona le schede dei circuiti LED. Le macchineposizionano quindi la barra luminosa preassemblata, la avvitano e la cablano.Infine, l'inserto luminoso viene programmato in modo completamente automatico.La combinazione di assemblaggio manuale e processi automatizzati produce da 900a 1.200 inserti per il sistema di illuminazione a file continue TECTON perturno.
Il lavoro manualedettagliato con specialisti ben addestrati rimarrà particolarmente importanteanche in futuro: “Perché non tutti i desideri dei nostri clienti possono essererealizzati con un sistema completamente automatizzato”, afferma il responsabiledel gruppo di produzione Michael Lassak. “Per noi rimane fondamentale averelinee di assemblaggio manuali che possano essere utilizzate per realizzareprogetti personalizzati”.
I cosiddetti“apparecchi speciali”, cioè quelli personalizzati in base alle esigenze deiclienti, rappresentano circa un quarto delle vendite del sito di Dornbirn, e latendenza è in aumento. Gli apparecchi personalizzati sono un importante puntodi forza degli esperti di illuminazione del Vorarlberg. “Soddisfiamo quasitutte le richieste dei clienti”, afferma il responsabile del gruppo diproduzione Michael Lassak. “Quasi ogni settimana, nel nostro reparto ci sonoprogettisti che vengono da noi con nuove idee e richieste dei clienti e con iquali creiamo dei campioni. È semplicemente emozionante ogni giorno”.
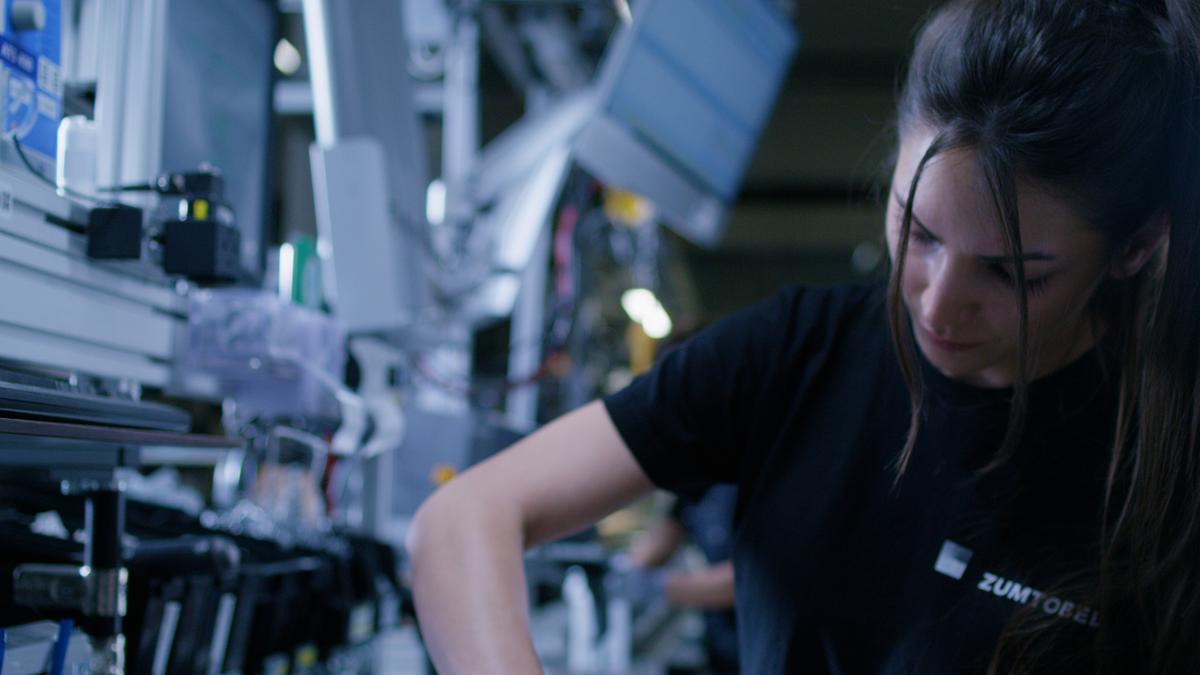
#2 Gli standard di qualità soddisfano la velocità di produzione
Qualsiasi deviazione dallostandard richiede anche un diverso flusso di lavoro. Michael Lassak spiega lesfide che devono affrontare i dipendenti della produzione: “A volte abbiamobisogno di dispositivi di assemblaggio diversi, le apparecchiature di provahanno bisogno di impostazioni diverse e dobbiamo ampliare i programmi di provaesistenti”. Del resto, gli standard di qualità di Zumtobel valgono anche pergli apparecchi personalizzati: Ogni prodotto, secondo la promessa del cliente,viene testato al 100% prima di lasciare la fabbrica di Dornbirn. Per garantireciò, in molti casi gli apparecchi Zumtobel non sono solo certificati ISO. Ilconcetto di “Tracebility”, proprio di Zumtobel, garantisce la totaletrasparenza del processo produttivo e crea standard di qualità vincolanti: Atal fine, ogni apparecchio viene dotato di un proprio codice QR, che vieneregistrato in ogni fase di produzione. Ogni parte installata in questa fase -che si tratti di LED o di convertitori - viene scansionata in anticipo eassegnata chiaramente all'apparecchio.
Alcuni controlli sonogià automatizzati, come ad esempio il controllo di qualità delle ottiche dellelenti TECTON. Zumtobel le produce dal granulato di plastica con un processo distampaggio a iniezione. Il granulato viene liquefatto a 320 gradi, iniettato epoi pressato. Prima che le ottiche finite vengano installate, una telecameraottica controlla i risultati della produzione, garantendo così che non venganoinstallati componenti con impurità, inclusioni o alterazioni della geometria.
Il nuovo sistema diproduzione di TECTON II è solo un esempio di come la gestione completa dellaqualità e le alte velocità di lavoro non si escludano a vicenda. La nuovagenerazione del collaudato sistema a file continue sarà lanciata sul mercatonella primavera del 2025 e sta già definendo gli standard nello stabilimento diDornbirn: “Il piano prevede che il nuovo sistema produca una volta e mezza inpiù rispetto al vecchio sistema nello stesso periodo”, rivela il responsabiledel gruppo di produzione Michael Lassak. Il nuovo TECTON II è tecnicamenteancora più sofisticato del precedente apparecchio TECTON C”. Nel progettare ilnuovo sistema e le linee di assemblaggio manuali, abbiamo quindi guardatoesplicitamente alle sfide del passato e ci siamo chiesti: cosa possiamoimparare da esse? Come possiamo ottimizzare la produzione di TECTON II?”.L'ampia esperienza acquisita in oltre 20 anni è stata quindi incorporata in unimpianto di produzione all'avanguardia.
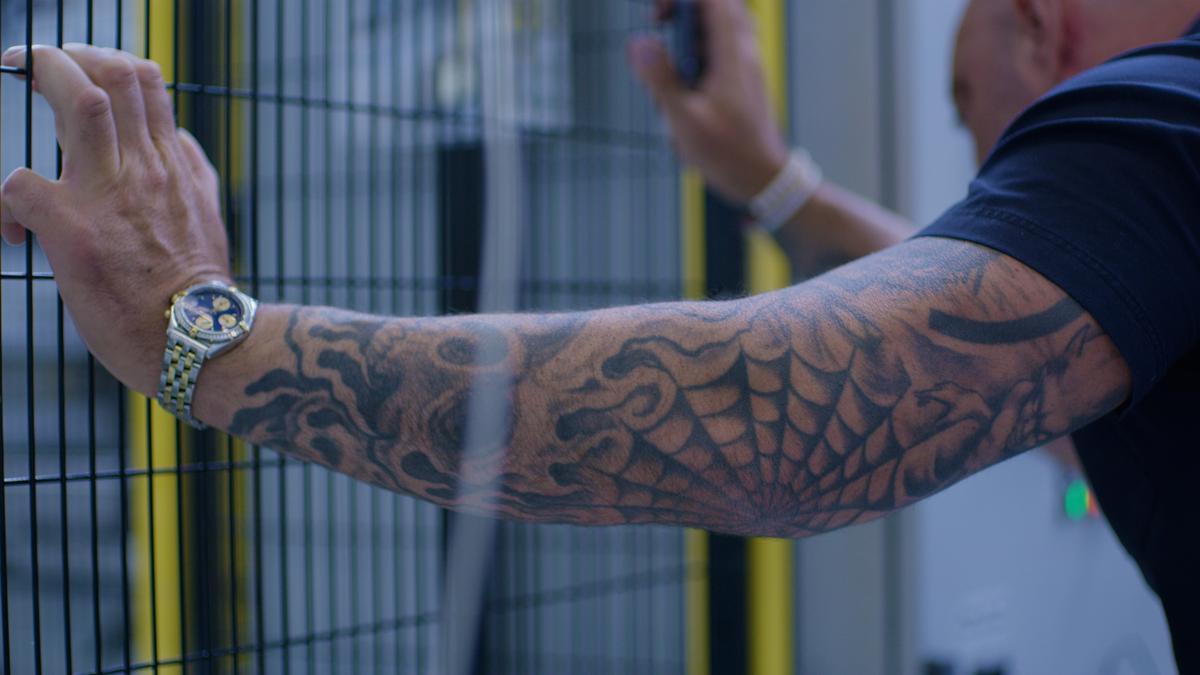
#3 La nuova edizioneincontra la compatibilità con il passato
In termini disostenibilità, tuttavia, l'era TECTON II non rompe con il passato. Questogarantisce la compatibilità con la generazione precedente ed è particolarmenteindicato per i progetti di ristrutturazione. Il binario TECTON esistenterimane, l'apparecchio aggiornato arriva: Michael Lassak e il team TECTON hannogià realizzato con successo progetti basati su questo principio: “Un buoncliente voleva adattare i nuovi apparecchi TECTON C al suo sistema dicanalizzazione esistente. Per me e per i miei colleghi è stata una sfida,perché dovevamo combinare il vecchio sistema con quello nuovo e creare unfascio di luce corrispondente. Il fatto che siamo riusciti a farlo ha reso ilnostro cliente molto felice alla fine”.
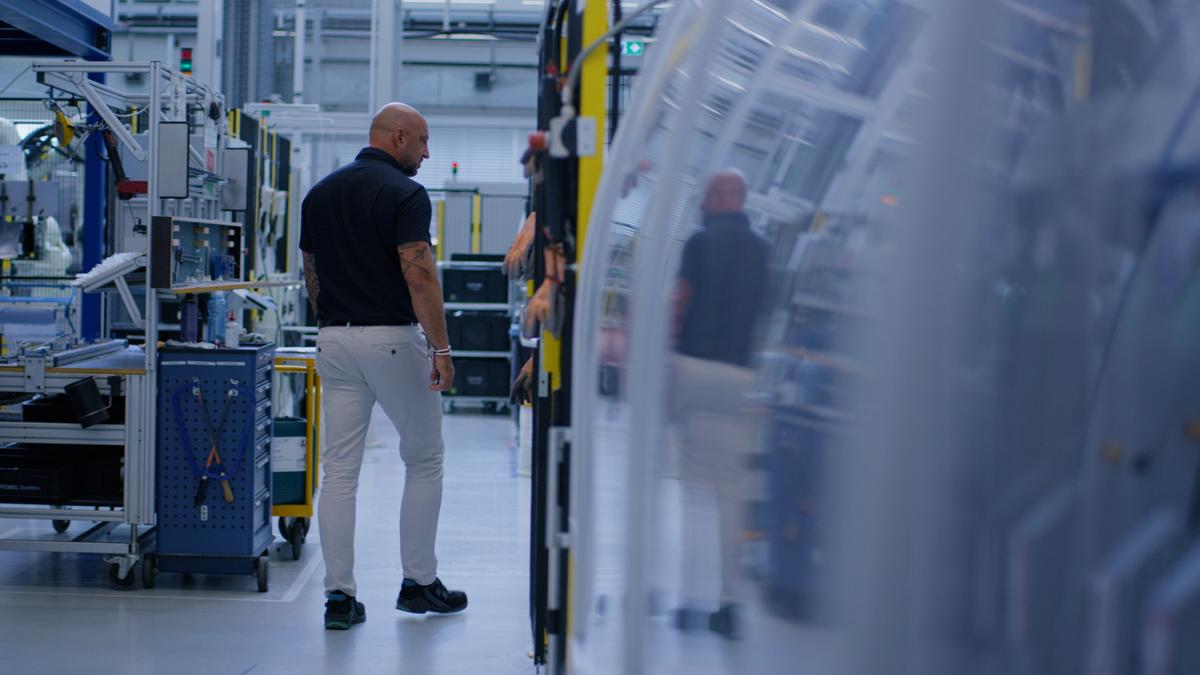
In breve, la nuovagenerazione di TECTON II mantiene la stessa incondizionata attenzione alcliente. Questo rende i sistemi esistenti assolutamente a prova di futuro,sostenibili e con un risparmio di risorse. Automazione e assemblaggio manuale.Standard di qualità e velocità di produzione. Nuove versioni e compatibilitàcon il passato. Apparenti opposti combinati in un sistema sofisticato: forsequesto è uno dei principali segreti del successo della produzione TECTON aDornbirn.