Made in Austria: Bis heute zählt TECTON zu den meistgefragten Produktfamilien im Zumtobel Portfolio – und wird im Werk in Dornbirn gefertigt. Kein Wunder, war TECTON doch weltweit das erste Lichtbandsystem mit 11-poligem in die Tragschiene integriertem Stromleitprofil. Es bildet die Basis für Allgemeinbeleuchtung, Sicherheits- und Notbeleuchtung sowie Lichtsteuerung. Eine Schiene, (fast) unendliche Möglichkeiten.
Doch bis TECTON bei den Kundinnen und Kunden vor Ort als multifunktionales Lichtbandsystem eingesetzt wird, sind einige Produktionsschritte notwendig. Stahlblechschienen stanzen, profilieren und verdrahten, Linsenoptik im Spritzgussverfahren fertigen, Lichteinsatz für die Tragschiene produzieren. Michael Lassak hat jeden einzelnen Fertigungsschritt im Blick. Als Production Group Leader bei der Zumtobel Group verantwortet er unter anderem die TECTON Produktion in Dornbirn – und teilt aus seiner Erfahrung „hinter den Kulissen“ drei überraschende Einsichten.
#1 Automatisierung trifft Handmontage
Ein Teil der TECTON Produktion läuft bereits voll automatisiert ab. Tatsächlich ist aber auch echte Handmontage von derzeit knapp 80 TECTON Mitarbeitenden gefragt. So werden die TECTON Schienen in drei Schichten teilautomatisch produziert. Die Mitarbeitenden legen lediglich die Kunststoffschienen ein, die restliche Fertigung und Verdrahtung der Schienen übernehmen die Maschinen.
Für die Produktion des TECTON Lichteinsatzes montieren die Mitarbeitenden händisch Komponenten auf dem Lichtbalken. Danach übernehmen autonome Roboterzellen: Ein Roboter holt Linsenoptiken aus einem Gebinde und platziert diese mithilfe einer Kamera. Ein weiterer Roboter legt LED Platinen auf. Anschließend setzen die Maschinen den vormontierten Lichtbalken auf, verschrauben und verdrahten diesen. Zum Schluss wird der Lichteinsatz noch vollautomatisch programmiert. In der Kombination von händischer Montage und automatisierten Abläufen entstehen pro Schicht 900 bis 1.200 Einsätze für das TECTON Lichtbandsystem.
Auch in Zukunft bleibt die handwerkliche Detailarbeit mit gut ausgebildetem Fachpersonal besonders wichtig: „Denn nicht alle Wünsche unserer Kunden lassen sich auf der vollautomatisierten Anlage umsetzen“, sagt Production Group Leader Michael Lassak.„Für uns bleibt es ein Muss, dass wir Handmontage-Linien bei uns haben, mit denen sich kundenindividuelle Projekte realisieren lassen.“
Sogenannte „Sonderleuchten“, also nach Kundenwünschen maßgeschneiderte Leuchten, machen zirka ein Viertel des Umsatzes am Standort Dornbirn aus –Tendenz steigend. Sonderleuchten sind ein wichtiges Alleinstellungsmerkmal der Vorarlberger Lichtexpertinnen und -experten. „Wir erfüllen so gut wie jeden Kundenwunsch, der an uns herangetragen wird“, sagt Production Group Leader Michael Lassak. „Beinahe wöchentlich haben wir Konstrukteure bei uns im Bereich, die mit neuen Ideen und Kundenanforderungen zu uns kommen und mit denen wir dann Muster erstellen. Es ist einfach jeden Tag spannend.“
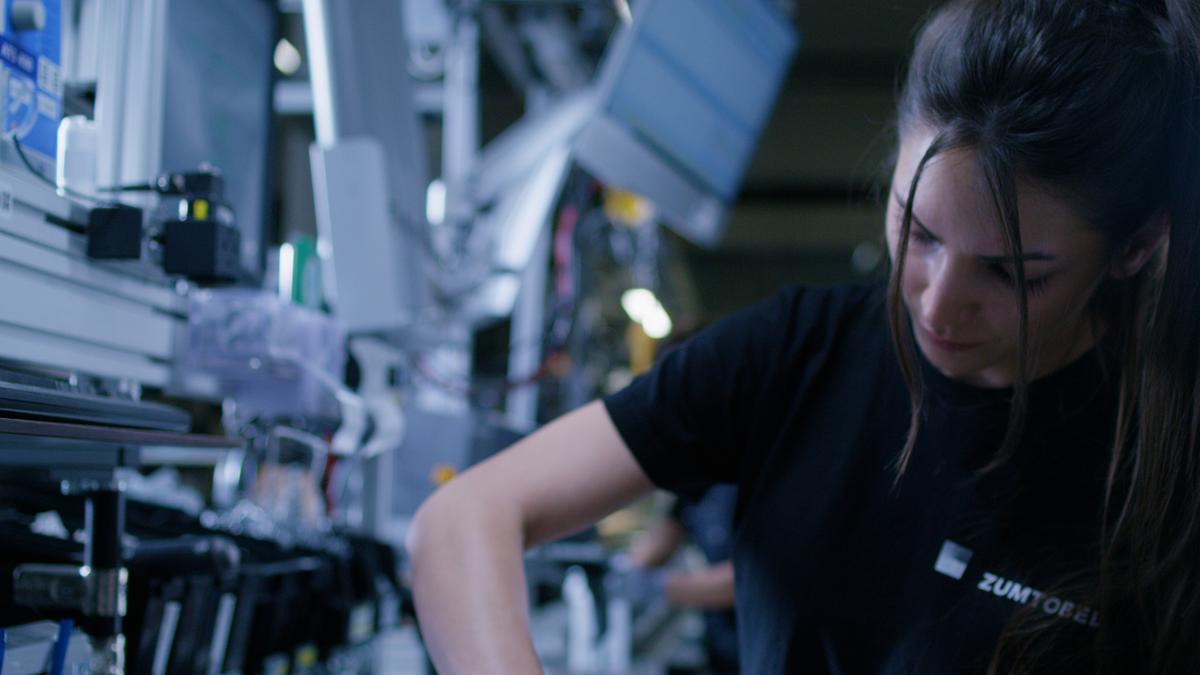
#2 Qualitätsanspruch trifft Produktionsgeschwindigkeit
Jede Abweichung vom Standard erfordert auch einen abweichenden Arbeitsablauf. Michael Lassak erklärt, vor welche Herausforderungen die Mitarbeitenden in der Produktion gestellt werden: „Wir benötigen teilweise andere Montagevorrichtungen, die Prüfgeräte brauchen andere Einstellungen und wir müssen die bestehenden Prüfprogramme erweitern.“ Schließlich gilt der Zumtobel Qualitätsanspruch auch für kundenindividuell gefertigte Leuchten: Jedes Produkt, so das Kundenversprechen, wird zu 100 Prozent geprüft, bevor es das Werk in Dornbirn verlässt. Damit das gelingt, sind Zumtobel Leuchten nicht nur vielfach ISO-zertifiziert. Ein Zumtobel eigenes „Tracebility“ Konzept sorgt für lückenlose Transparenz im Produktionsablauf und schafft verbindliche Qualitätsstandards: Dafür erhält jede Leuchte einen eigenen QR-Code, der bei jedem Fertigungsschritt erfasst wird. Jedes eingebaute Teil in dem Schritt – ob LEDs oder Converter – wird vorher gescannt und eindeutig der Leuchte zugeordnet.
Ein Teil der Kontrollen läuft bereits automatisiert ab, zum Beispiel die Qualitätsprüfung der TECTON Linsenoptik. Diese stellt Zumtobel aus Kunststoffgranulat im Spritzgussverfahren her. Dafür wird das Granulat bei 320 Grad verflüssigt, gespritzt und anschließend gepresst. Bevor die fertigen Optiken verbaut werden, sichtet eine optische Kamera die Produktionsergebnisse – und sorgt so dafür, dass keine Komponenten mit Verunreinigungen, Einschlüssen oder Geometrieänderungen verbaut werden.
Dass umfassendes Qualitätsmanagement und hohe Arbeitsgeschwindigkeit sich nicht ausschließen, beweist unter anderem die neue Produktionsanlage für TECTON II. Die neue Generation des bewährten Lichtbandsystems soll im Frühjahr 2025 auf den Markt kommen – und setzt schon jetzt Standards innerhalb des Werks in Dornbirn: „Geplant ist, dass die neue Anlage im selben Zeitraum eineinhalb Mal so viel produziert wie die alte Anlage“, verrät Production Group Leader Michael Lassak. „Die Neuauflage TECTON II ist technisch noch einmal anspruchsvoller als die bisherige TECTON C Leuchte. Für die Konstruktion der neuen Anlage und der Handmontage-Linien haben wir deshalb explizit noch einmal auf die Herausforderungen der Vergangenheit geblickt und uns gefragt: Was können wir daraus lernen? Wie können wir die Fertigung von TECTON II optimal gestalten?“ Umfassende Erfahrungen aus mehr als 20 Jahren sind so in das State-of-the-Art Produktions-Setup eingeflossen.
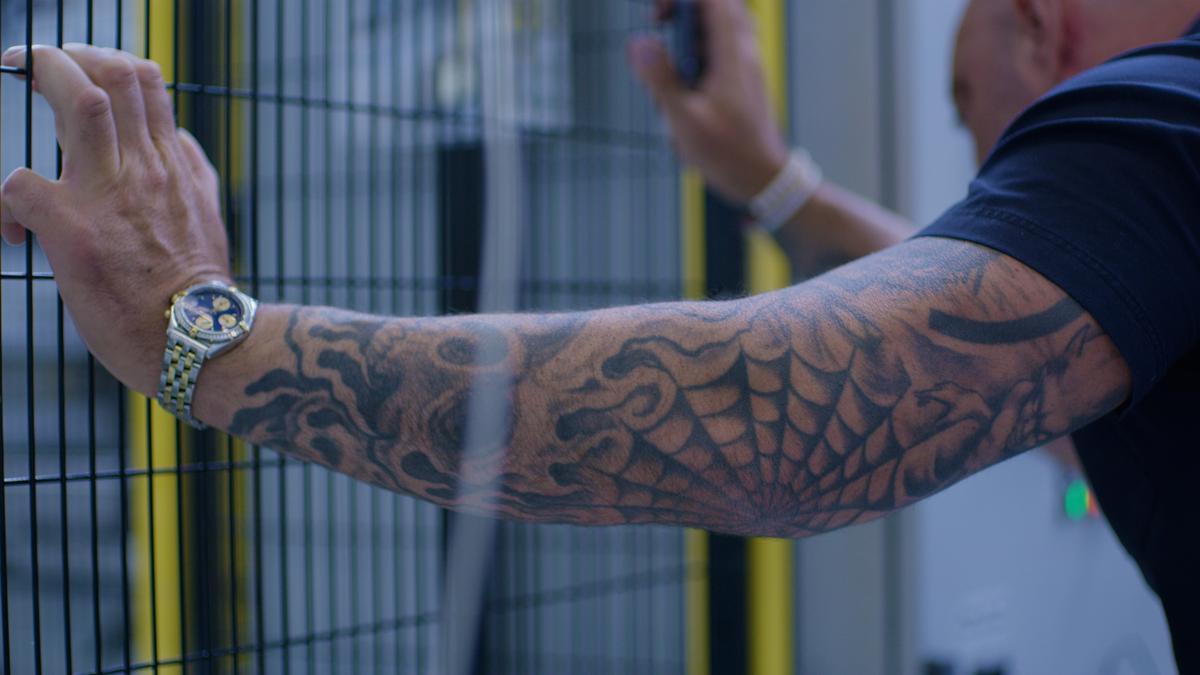
#3 Neuauflage trifft Rückwärtskompatibilität
Im Sinne der Nachhaltigkeit werden mit der TECTON II Ära jedoch nicht die Verbindungen in die Vergangenheit gekappt. Dafür sorgt die Rückwärtskompatibilität des Systems, das sich insbesondere auch für Sanierungsprojekte eignet. Die TECTON Bestandsschiene bleibt, die aktualisierte Leuchte kommt: Nach diesem Prinzip hat Michael Lassak mit dem TECTON Team in der Vergangenheit bereits erfolgreiche Projekte umgesetzt: „Ein guter Kunde wollte die damals neuen TECTON C Leuchten auf sein bestehendes Tragschienensystem angepasst haben. Eine kleine Herausforderung für meine Mitarbeitenden und mich, denn wir mussten das alte System mit dem neuen verheiraten – und einen passenden Balken erstellen. Dass das gelungen ist, hat unseren Kunden am Ende glücklich gemacht.“
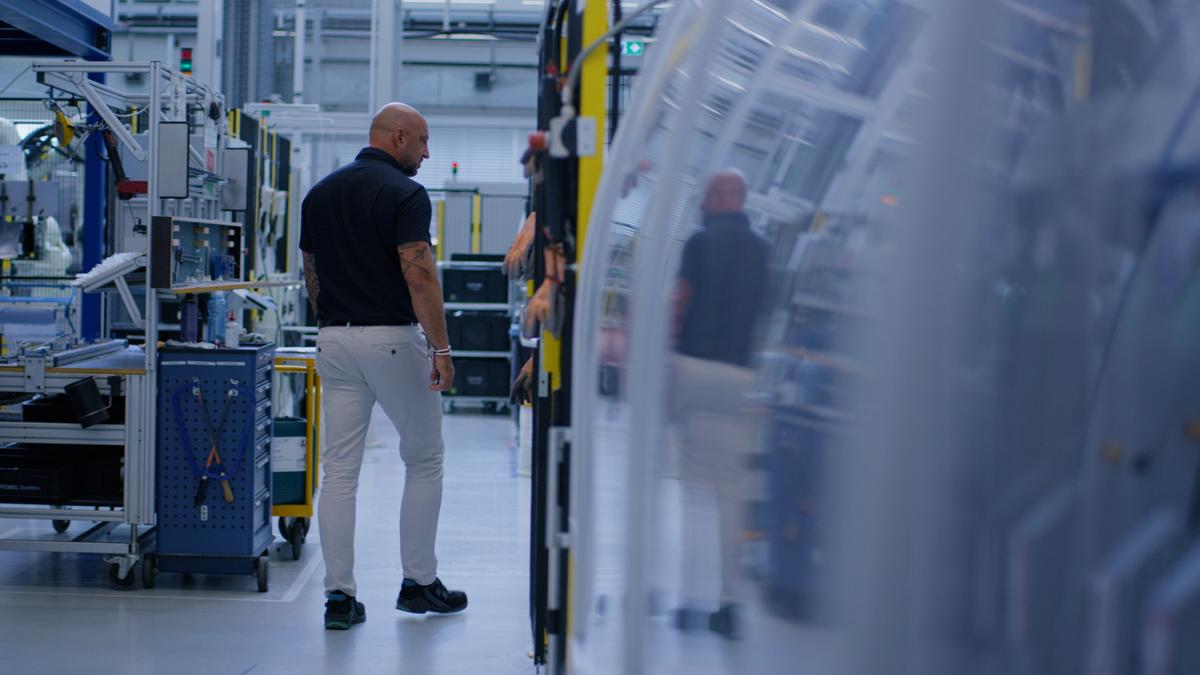
Fazit: Die unbedingte Kundenorientierung bleibt auch mit der neuen Generation TECTON II erhalten. Schon jetzt steht fest, dass die TECTON II Leuchte rückwärtskompatibel ist – und somit auch Bestandsanlagen absolut zukunftssicher, nachhaltig und ressourcenschonend nutzbar macht. Automatisierung und Handmontage. Qualitätsanspruch und Produktionsgeschwindigkeit. Neuauflage und Rückwärtskompatibilität. Scheinbare Gegensätze in einem durchdachten System vereint: Vielleicht ist gerade das eines der wesentlichen Erfolgsgeheimnisse der TECTON Produktion in Dornbirn.