Made in Austria: TECTONis still one of the most popular product families in the Zumtobel portfolio -and is manufactured at the Dornbirn plant. No wonder, since TECTON was theworld's first continuous-row lighting system with an 11-pole conductor profileintegrated in the trunking. It forms the basis for general lighting, safety andemergency lighting as well as lighting control. One track, (almost) endlesspossibilities.
But before TECTON canbe used by the customer as a multifunctional continuous-row lighting system,several production steps are necessary. These include punching, profiling andwiring the sheet steel tracks, manufacturing the lens optics by injection moulding,and producing the luminaire inserts for the trunking. Michael Lassak keeps aneye on each individual production step. As Production Group Leader in theZumtobel Group, his responsibilities include TECTON production in Dornbirn -and he shares three surprising insights from his experience "behind thescenes".
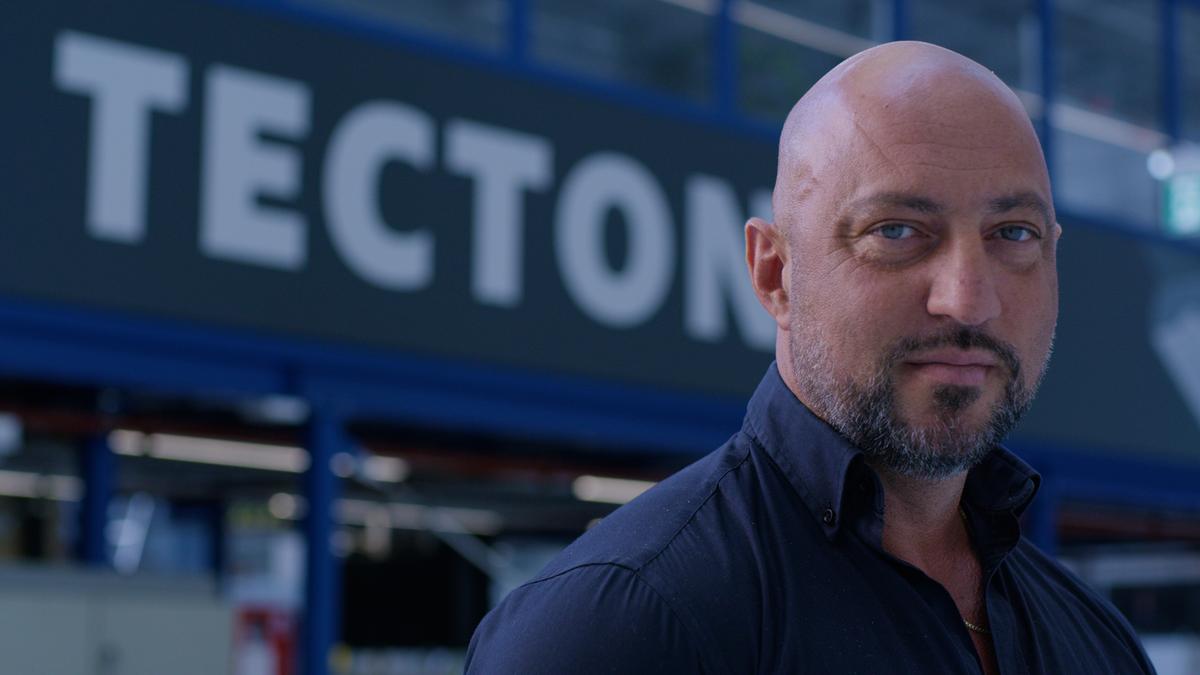
#1 Automation meets manual assembly
Part of the TECTONproduction process is already fully automated. However, the almost 80 TECTONemployees who currently work there also have to carry out genuine manualassembly. The TECTON tracks are produced semi-automatically in three shifts.The employees only insert the plastic tracks, the rest of the production andwiring of the tracks is done by the machines.
For the production ofthe TECTON light insert, the employees manually assemble the components on thelight rail. Autonomous robot cells then take over: One robot takes lens opticsfrom a container and places them with the aid of a camera. Another robot placesLED circuit boards. The machines then position, screw and wire thepre-assembled light bar. Finally, the light insert is programmed fullyautomatically. The combination of manual assembly and automated processesproduces between 900 and 1,200 inserts for the TECTON continuous-row lightingsystem per shift.
Detailed manual work bywell-trained specialists will remain particularly important in the future: 'Notall of our customers' wishes can be realised on the fully automated system,'says Production Group Leader Michael Lassak. For us, it remains a must to havemanual assembly lines that can be used to realise customer-specific projects.
So-called 'specialluminaires', i.e. luminaires tailored to customer requirements, account foraround a quarter of sales at the Dornbirn site - and the trend is rising.Customised luminaires are an important unique selling point for the Vorarlberglighting experts. We fulfil almost every customer request that comes our way,'says Production Group Manager Michael Lassak. Almost every week we havedesigners in our department who come to us with new ideas and customerrequirements, and with whom we then create samples. It's exciting every day.
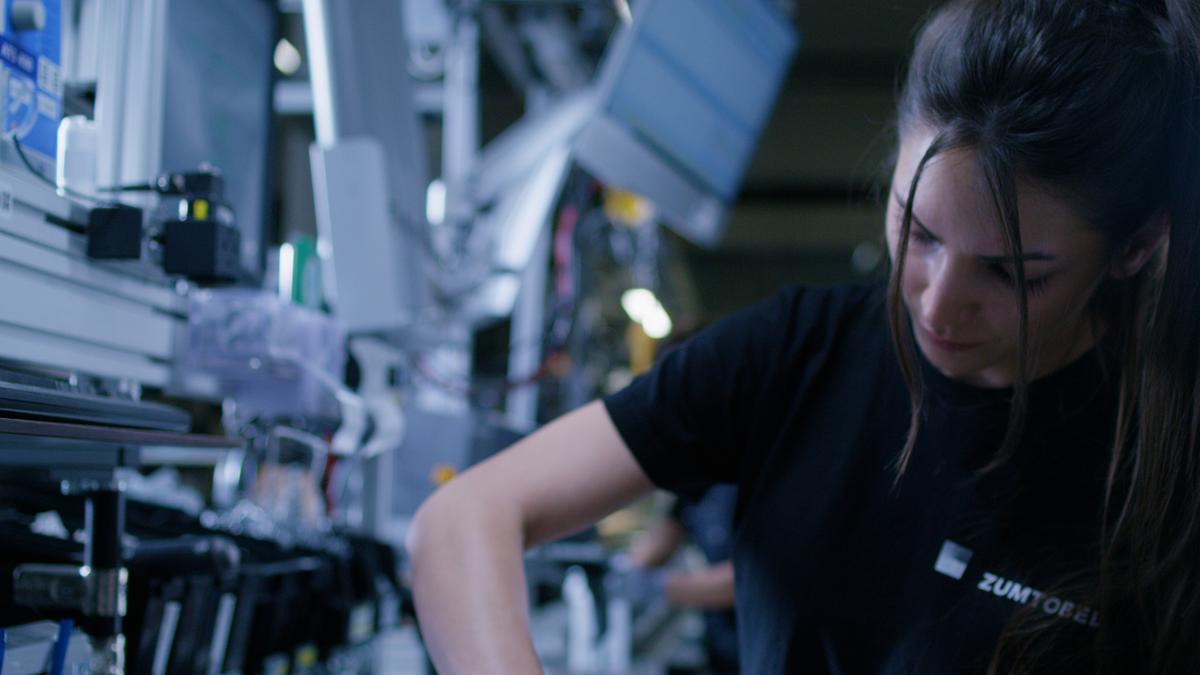
#2 Quality standards meet production speed
Any deviation from thestandard also requires a different workflow. Michael Lassak explains thechallenges faced by the production staff: "We sometimes need differentassembly equipment, the test equipment needs different settings and we have toextend the existing test programmes. After all, Zumtobel's quality standardsalso apply to customised luminaires: Every product is 100 per cent testedbefore it leaves the factory in Dornbirn, as promised to the customer. Toensure this, Zumtobel luminaires are not only ISO-certified in many cases.Zumtobel's own "Tracebility" concept ensures complete transparency inthe production process and creates binding quality standards: To this end, eachluminaire is given its own QR code, which is recorded at each production step.Every component used in this step - whether LEDs or converters - is scannedbeforehand and clearly assigned to the luminaire.
Some tests are alreadyautomated, such as the quality inspection of the TECTON lens optics. Zumtobelproduces these from plastic granulate using an injection moulding process. Thegranulate is liquefied at 320°C, injected and then pressed. Before the finishedoptics are installed, an optical camera inspects the production result, thusensuring that no components with impurities, inclusions or changes in geometryare installed.
The new productionsystem for TECTON II is just one example of how comprehensive qualitymanagement and high working speeds are not mutually exclusive. The newgeneration of the tried-and-tested inline system is due to be launched on themarket in spring 2025 - and is already setting standards at the Dornbirn plant:'The plan is for the new system to produce one and a half times as much as theold system in the same period of time,' reveals Production Group ManagerMichael Lassak. The new TECTON II is technically even more sophisticated thanthe previous TECTON C luminaire. When designing the new system and the manualassembly lines, we therefore explicitly looked back at the challenges of thepast and asked ourselves: What can we learn from them? How can we optimise theproduction of TECTON II? As a result, more than 20 years of experience havebeen incorporated into the state-of-the-art production facility.
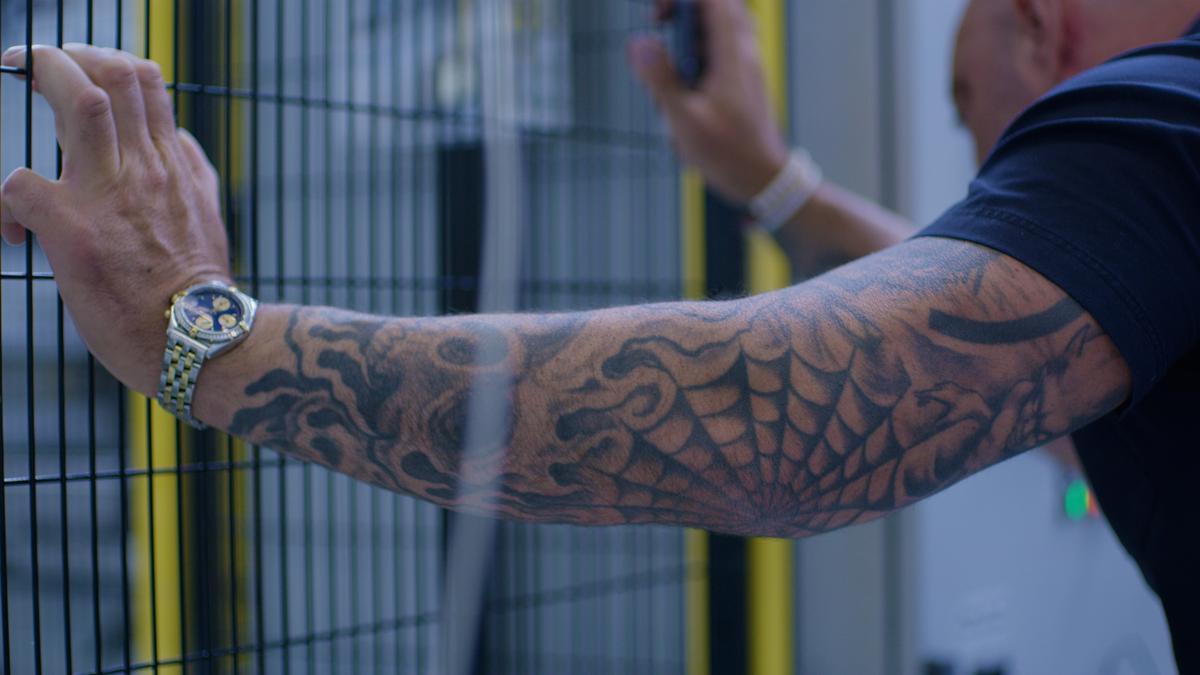
#3 new edition meets backwards compatibility
In terms ofsustainability, however, the TECTON II era does not break with the past. Thisensures its compatibility with the previous generation and is particularlysuitable for refurbishment projects. The existing TECTON track stays, theupdated luminaire comes: Michael Lassak and the TECTON team have alreadysuccessfully implemented projects based on this principle in the past: "Agood customer wanted to adapt the new TECTON C luminaires to his existing trunkingsystem. That was a bit of a challenge for me and my colleagues, because we hadto combine the old system with the new one - and create a matching beam. Thefact that we managed to do this made our customer very happy in the end.“
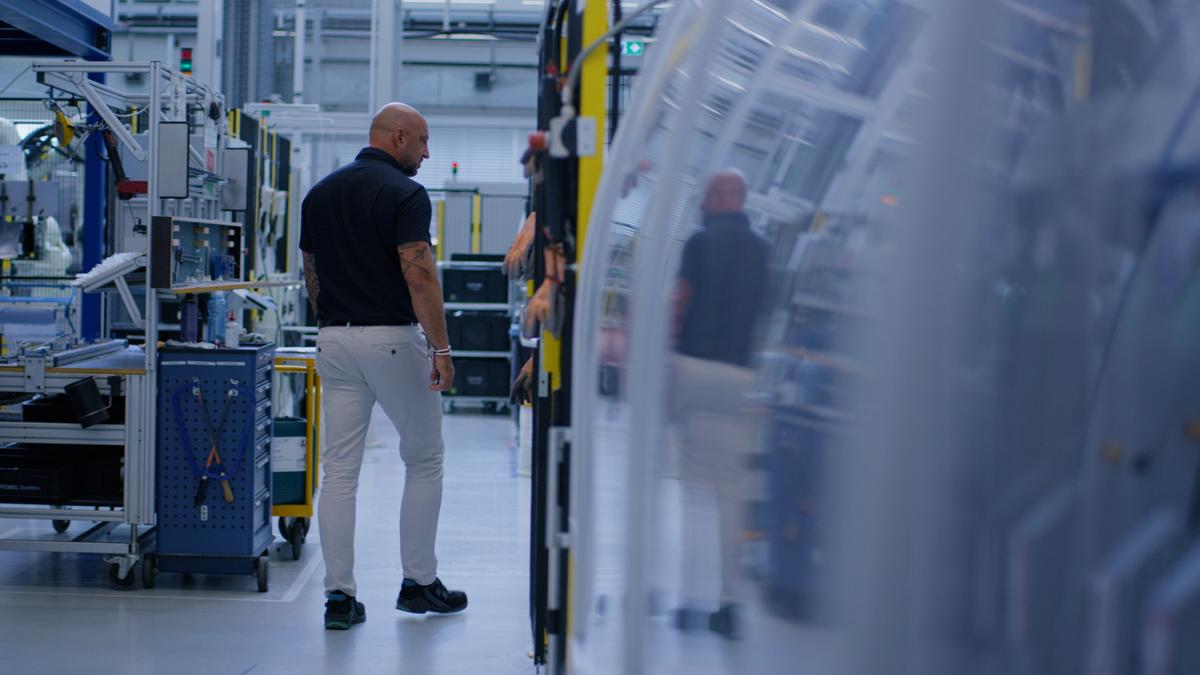
In short, the newTECTON II generation retains the same unconditional customer focus. This makesexisting systems absolutely future-proof, sustainable and saves resources.Automation and manual assembly. Quality standards and production speed. Newversions and backwards compatibility. Apparent opposites combined in asophisticated system: perhaps this is one of the main secrets of the success ofTECTON production in Dornbirn.