Made in Austria: TECTON behoort tot op vandaag nog steeds tot depopulairste productfamilies van Zumtobel - en wordt in de fabriek in Dornbirngeproduceerd. Niet verwonderlijk, want TECTON was wereldwijd het eerstelichtlijnsysteem met de ononderbroken, in de draagrail geïntegreerde 11-poligegeleiders. Het vormt de basis voor algemene verlichting, veiligheids- ennoodverlichting en lichtsturing. Eén rail, (bijna) onbeperkte mogelijkheden.
Maar vooraleer TECTON door de klant als multifunctioneel lichtlijnsysteemkan worden gebruikt, zijn er verschillende productiestappen nodig. Dit omvathet stansen, profileren en bedraden van de rails uit plaatstaal, hetspuitgieten van de lensoptieken en de productie van de armatuurelementen voorde draagrails. Michael Lassak houdt daarbij alle afzonderlijke productiestappennauwlettend onder controle. Als Production Group Leader van de Zumtobel Groupis hij onder meer verantwoordelijk voor de TECTON-productie in Dornbirn - enhij deelt drie verrassende inzichten vanuit zijn ervaring "achter deschermen".
#1 Automatisering ontmoethandmatige assemblage
Een deel van de TECTON-productie verloopt al volledig geautomatiseerd. Tochis er nog steeds vraag naar handmatige montage door de bijna 80TECTON-medewerkers. Zo worden de TECTON-rails in drie ploegen semi-automatischgeproduceerd. De medewerkers plaatsen alleen de kunststofrails, de rest van deproductie en bedrading van de rails wordt door de machines gedaan.
Voor de productie van de TECTON-lichtelementen monteren de medewerkershandmatig componenten op de lichtbalk. Daarna nemen autonome robotcellen hetover: een robot haalt lenzenoptieken uit een verpakking en plaatst deze metbehulp van een camera. Een andere robot plaatst LED-printplaten. Vervolgenszetten de machines de voorgemonteerde lichtbalk op, schroeven en bedraden deze.Tot slot wordt het lichtelement volledig automatisch geprogrammeerd. Dankzij decombinatie van handmatige montage en geautomatiseerde processen worden er perploeg 900 tot 1.200 armatuurelementen voor het TECTON-lichtbandsysteemgeproduceerd.
Ook in de toekomst blijft handmatig gedetailleerd werk door goed opgeleidpersoneel bijzonder belangrijk: "Want niet alle wensen van onze klantenkunnen op de volledig geautomatiseerde installatie worden uitgevoerd,"zegt Productiegroepsleider Michael Lassak. "Voor ons is het een vereisteom handmontagelijnen te hebben waarmee we klantgerichte projecten kunnenrealiseren."
Zogenaamde 'speciale verlichtingsarmaturen', oftewel op maat gemaakteverlichtingsarmaturen volgens klantwensen, maken ongeveer een kwart van deomzet in de vestiging in Dornbirn uit, en dit aandeel groeit. Specialeverlichtingsarmaturen zijn een belangrijk uniek verkoopargument van delichtspecialisten in Vorarlberg. "We voldoen aan vrijwel elke klantwensdie bij ons binnenkomt," zegt Productiegroepsleider Michael Lassak."Bijna wekelijks hebben we constructeurs bij ons die met nieuwe ideeën enklantvereisten komen, en met hen maken we dan prototypes. Het is gewoon elkedag opnieuw boeiend.”
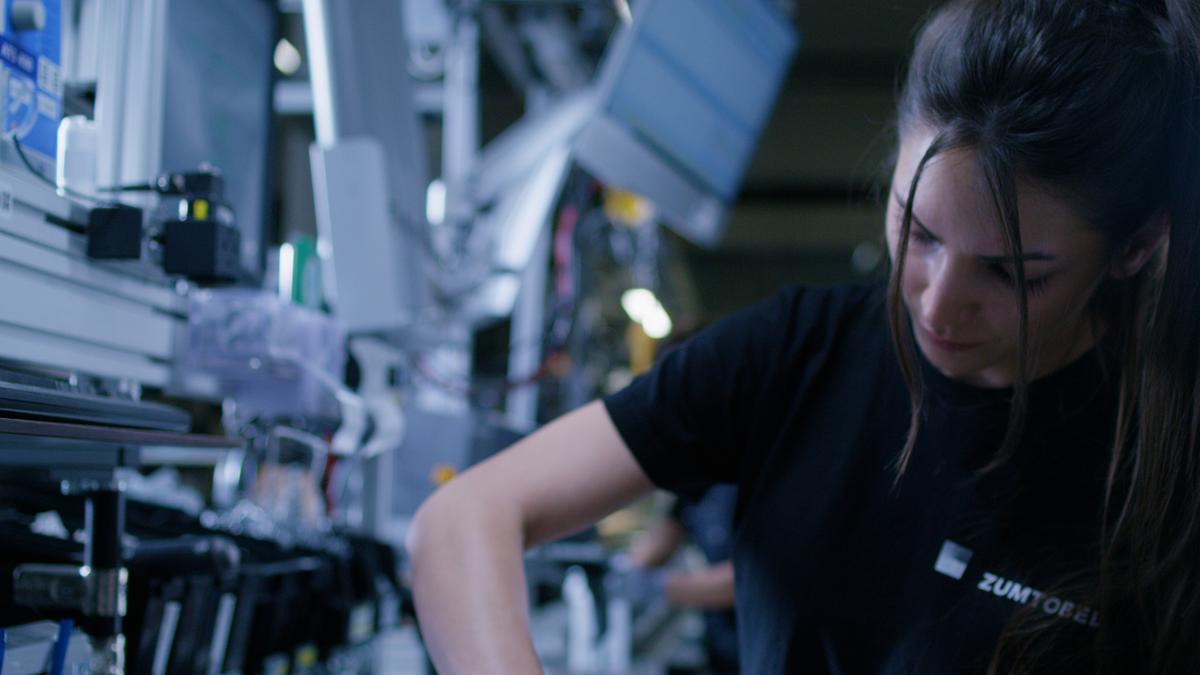
#2 Kwaliteitsnormen voldoen aan productiesnelheid
Elke afwijking van de standaard vereist een aangepaste werkwijze. MichaelLassak legt uit voor welke uitdagingen de medewerkers in de productie staan:“We hebben soms andere montagemiddelen nodig, de testapparatuur vereist andereinstellingen en we moeten de bestaande testprogramma's uitbreiden.” Dekwaliteitseisen van Zumtobel gelden ook voor op maat gemaakteverlichtingsarmaturen: Elk product wordt, zoals beloofd aan de klant, voor 100%gecontroleerd voordat het de fabriek in Dornbirn verlaat. Om dit te bereiken,zijn Zumtobel-verlichtingsarmaturen niet alleen op veel vlakkenISO-gecertificeerd. Een eigen "Traceability"-concept van Zumtobelzorgt voor volledige transparantie in het productieproces en creëert bindendekwaliteitsnormen. Elk armatuur krijgt een eigen QR-code die bij elkeproductiestap wordt gescand. Elk ingebouwd onderdeel in die stap – of het nugaat om LED’s of converters – wordt vooraf gescand en eenduidig aan de armatuurtoegewezen.
Een deel van de controles verloopt al geautomatiseerd, zoals dekwaliteitscontrole van de TECTON-lensoptiek. Deze wordt door Zumtobel uitkunststofgranulaat geproduceerd via spuitgieten. Het granulaat wordt bij 320°Cvloeibaar gemaakt, gespoten en vervolgens geperst. Voordat de afgewerkteoptieken worden gemonteerd, controleert een optische camera deproductieresultaten, zodat geen componenten met verontreinigingen, insluitingenof geometrische afwijkingen worden gebruikt.
Dat uitgebreid kwaliteitsbeheer en hoge productiesnelheid hand in handkunnen gaan, bewijst onder andere de nieuwe productielijn voor TECTON II. Denieuwe generatie van het beproefde lichtbandsysteem komt in het voorjaar van2025 op de markt en zet nu al normen binnen de fabriek in Dornbirn. “Het is debedoeling dat de nieuwe lijn in dezelfde tijd anderhalf keer zoveel produceertals de oude lijn,” onthult Productiegroepsleider Michael Lassak. “De nieuweTECTON II is technisch nog veeleisender dan de huidige TECTON C-armatuur.Voor de constructie van de nieuwe lijn en de handmontagelijnen hebben we daaromexpliciet naar de uitdagingen uit het verleden gekeken en ons afgevraagd: Watkunnen we hiervan leren? Hoe kunnen we de productie van TECTON II optimaalvormgeven?” Uitgebreide ervaring van meer dan 20 jaar is zo verwerkt in destate-of-the-art productieopstelling.
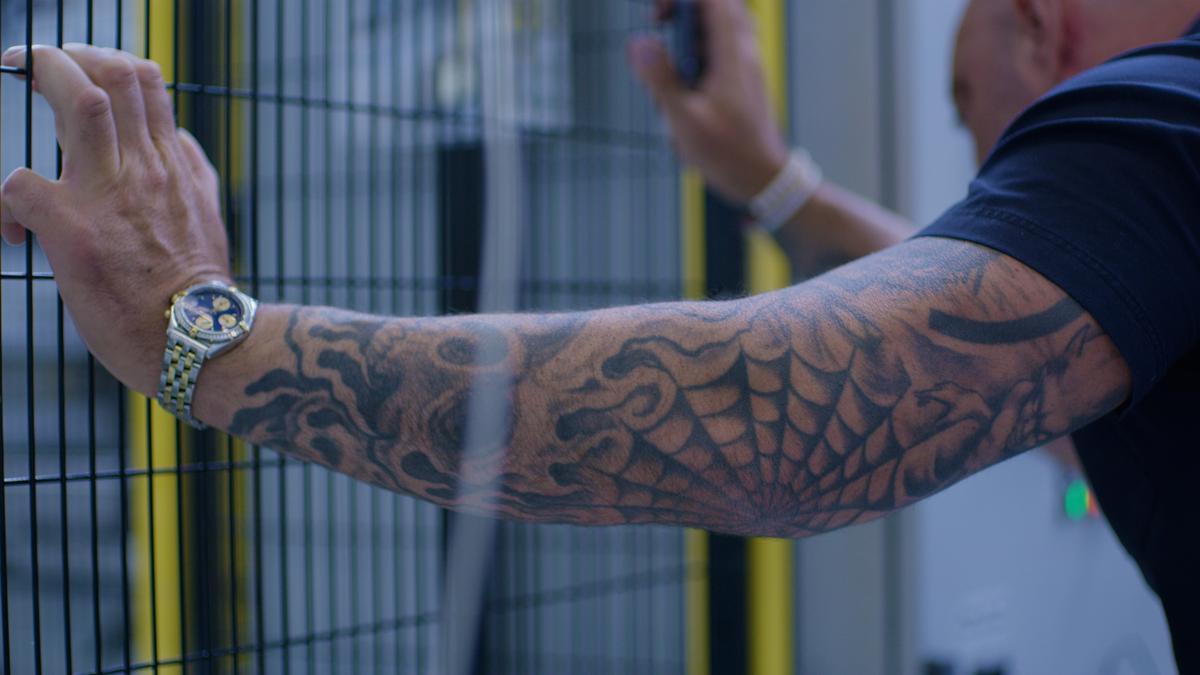
#3 Nieuwe editie ontmoetachterwaartse compatibiliteit
Het TECTON II tijdperk verbreekt de banden met het verleden echter niet ophet vlak van duurzaamheid. Daarvoor zorgt de achterwaartse compatibiliteit vanhet systeem, die bijzonder geschikt is voor renovatieprojecten. De bestaande TECTON-railblijft, de geactualiseerde armatuur komt: Michael Lassak en het TECTON-teamhebben in het verleden al succesvolle projecten volgens dit principegerealiseerd: “Een goede klant wilde de toen nieuwe TECTON-C armaturen aan zijnbestaande draagrailsysteem aanpassen. Het was een uitdaging voor mijnmedewerkers en voor mij, want we moesten het oude systeem met het nieuweverenigen - en een passende lichtoplossing creëren. Het feit dat we daaringeslaagd zijn, maakte onze klant uiteindelijk blij.”
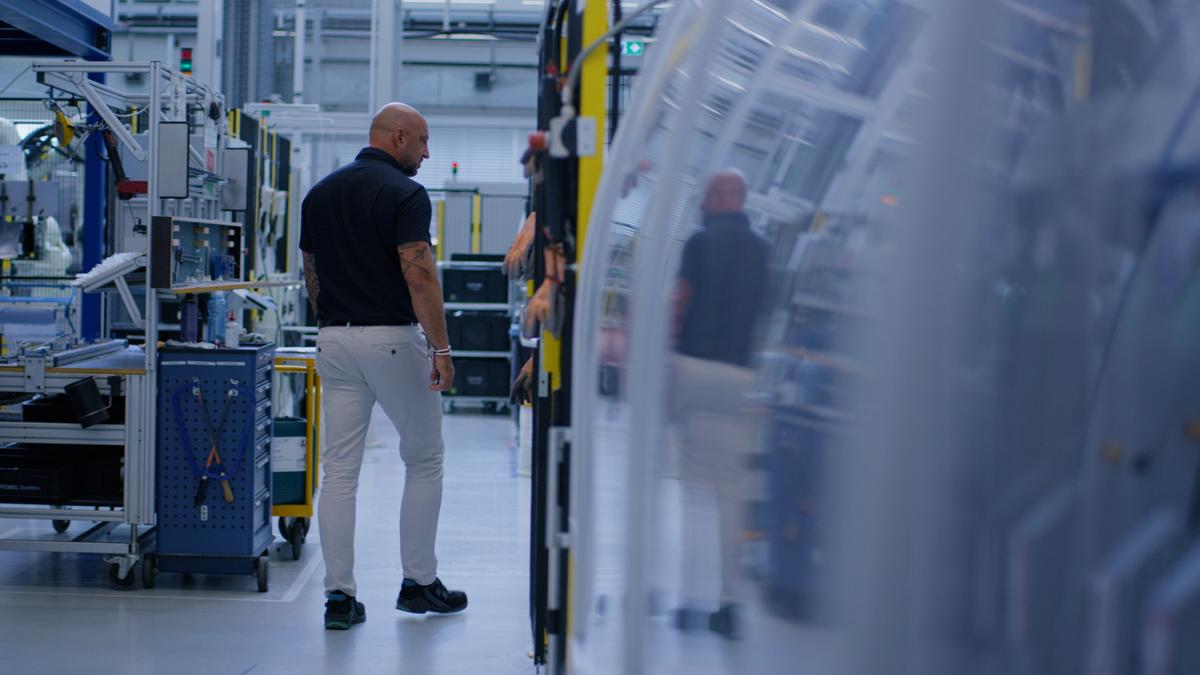
In het kader van duurzaamheid worden met de TECTON II- era echter niet debanden met het verleden doorgesneden. De achterwaartse compatibiliteit van hetsysteem zorgt ervoor dat het bijzonder geschikt is voor renovatieprojecten. Debestaande TECTON-rail blijft, terwijl de vernieuwde armatuur komt: volgens ditprincipe heeft Michael Lassak met het TECTON-team in het verleden alsuccesvolle projecten uitgevoerd. “Een goede klant wilde destijds de nieuweTECTON-C armaturen aanpassen aan zijn bestaande draagrailsysteem. Een uitdagingvoor mijn medewerkers en voor mij, want we moesten het oude systeem met hetnieuwe verbinden en een geschikte lichtbalk creëren. Het feit dat dit isgelukt, maakte onze klant uiteindelijk gelukkig.”
Conclusie: De onvoorwaardelijke klantgerichtheid blijft behouden met denieuwe generatie TECTON II. Nu al staat vast dat de TECTON II-armatuurachterwaarts compatibel is, waardoor bestaande installaties absoluuttoekomstbestendig, duurzaam en grondstofbesparend zijn. Automatisering enhandmontage. Kwaliteitseisen en productiesnelheid. Nieuwe editie enachterwaartse compatibiliteit. Schijnbare tegenstellingen verenigd in eendoordacht systeem: misschien is dat wel een van de belangrijkste succesgeheimenvan de TECTON-productie in Dornbirn.